Measuring the Subfloor Thickness in Mobile Homes: A Comprehensive Guide
The subfloor in a mobile home is a crucial component that provides structural support, insulation, and a base for flooring materials. Its thickness is a vital factor that affects the overall integrity and durability of the home.
Typically, subfloors in mobile homes range from 1/2 inch to 1 inch thick. The thickness is determined by the manufacturer and is designed to meet specific building codes and standards. A thicker subfloor enhances the home's structural strength, reduces noise transmission, and improves insulation, resulting in a more comfortable and energy-efficient living space.
How Thick Is The Subfloor In A Mobile
The thickness of the subfloor in a mobile home is a critical factor that affects the overall structural integrity and durability of the home. Several key aspects related to the thickness of the subfloor in a mobile home include:
- Structural Support
- Insulation
- Soundproofing
- Flooring Type
- Building Codes
- Manufacturer Specifications
- Climate Considerations
- Floor Plan
- Maintenance
The thickness of the subfloor in a mobile home impacts its ability to provide adequate support for the flooring and other structural components, regulate temperature and reduce heat loss, minimize noise transmission, accommodate different types of flooring materials, meet building code requirements, adhere to manufacturer guidelines, withstand regional climate conditions, support the home's floor plan, and influence the maintenance and repair needs of the home.
Structural Support
Structural support is a critical component of the subfloor in a mobile home. The thickness of the subfloor directly affects its ability to provide adequate support for the flooring and other structural components. A thicker subfloor provides greater strength and rigidity, reducing the risk of deflection, sagging, or buckling under heavy loads or foot traffic.
In mobile homes, the subfloor is typically made of plywood or oriented strand board (OSB), with a thickness ranging from 1/2 inch to 1 inch. The thicker the subfloor, the more weight it can support and the less likely it is to warp or crack over time. This is especially important in areas with high levels of moisture or humidity, as these conditions can weaken the subfloor and compromise its structural integrity.
Real-life examples of the importance of structural support in mobile homes include preventing damage to flooring materials, such as tiles, hardwood, or vinyl, which can crack or break if the subfloor is too thin or weak. A properly supported subfloor also ensures that walls and other structural elements remain stable and aligned, preventing premature wear and tear or even structural failure.
Understanding the connection between structural support and the thickness of the subfloor in a mobile home is crucial for ensuring the longevity and safety of the structure. By choosing a subfloor with an appropriate thickness, homeowners can protect their investment and maintain the integrity of their mobile home for years to come.
Insulation
Insulation plays a crucial role in the overall energy efficiency and comfort of a mobile home. The thickness of the subfloor can impact the effectiveness of the insulation, as a thicker subfloor provides more space for insulating materials.
- Thermal Insulation
A thicker subfloor allows for more insulation to be installed, reducing heat loss during cold weather and improving energy efficiency. This can result in lower heating costs and a more comfortable living environment.
- Acoustic Insulation
A thicker subfloor can also help to reduce noise transmission between rooms and from outside sources. This can create a quieter and more peaceful living space.
- Moisture Control
A thicker subfloor can act as a barrier against moisture, preventing it from seeping into the home and causing damage to the flooring and other structural components.
- Fire Resistance
Some types of insulation materials, such as fiberglass, can also provide fire resistance. A thicker subfloor allows for more insulation to be installed, which can improve the fire safety of the home.
Overall, the thickness of the subfloor in a mobile home is an important consideration when it comes to insulation. A thicker subfloor allows for more insulation to be installed, which can improve energy efficiency, reduce noise, control moisture, and enhance fire resistance.
Soundproofing
As we delve into the topic of "How Thick Is The Subfloor In A Mobile", it's imperative to consider the aspect of soundproofing. The thickness of the subfloor plays a crucial role in reducing noise transmission, creating a more peaceful and comfortable living environment.
- Impact Noise
A thicker subfloor can help to reduce impact noise, such as footsteps or dropped objects, by absorbing and dampening the sound waves. This is especially important in multi-story mobile homes or those located near busy streets.
- Airborne Noise
A thicker subfloor can also help to reduce airborne noise, such as conversations or music, by blocking the sound waves from traveling through the floor and into other rooms. This can create a more private and serene living space.
- Vibration Isolation
A thicker subfloor can help to isolate vibrations from appliances or machinery, preventing them from being transmitted throughout the home. This can be especially beneficial in mobile homes with washer/dryer units or other vibrating appliances.
- Acoustic Insulation
Some types of subflooring materials, such as cork or rubber, have inherent acoustic insulation properties. A thicker subfloor made of these materials can provide even greater noise reduction.
In conclusion, the thickness of the subfloor in a mobile home is an important factor to consider when it comes to soundproofing. A thicker subfloor can help to reduce impact noise, airborne noise, vibration isolation, and provide acoustic insulation, creating a quieter and more comfortable living environment.
Flooring Type
Within the context of "How Thick Is The Subfloor In A Mobile", the flooring type is a critical component that directly influences the thickness and composition of the subfloor. The thickness of the subfloor must be adequate to support the weight and specific requirements of the flooring material being installed.
For instance, thicker subfloors are necessary for heavier flooring materials such as ceramic tiles or hardwood, as they require a more rigid and stable base to prevent deflection or damage. Conversely, thinner subfloors may be sufficient for lighter flooring options like vinyl or carpet, which are more flexible and can tolerate a less robust subfloor.
Understanding the relationship between flooring type and subfloor thickness is crucial for ensuring the longevity and performance of both the flooring and the subfloor itself. An appropriately thick subfloor provides a solid foundation for the flooring, preventing premature wear, cracking, or buckling. Conversely, an inadequate subfloor can compromise the integrity of the flooring, leading to costly repairs or replacements.
Building Codes
Building codes play a critical role in determining "How Thick Is The Subfloor In A Mobile". These codes are established by local, state, or national authorities to ensure the safety, structural integrity, and durability of buildings, including mobile homes. Building codes specify minimum requirements for various aspects of construction, including the thickness of the subfloor.
The thickness of the subfloor is directly related to the structural support it provides. A thicker subfloor is more rigid and can bear more weight without bending or sagging. Building codes specify minimum subfloor thickness based on the size, layout, and expected loads of the mobile home. Failure to meet these requirements can compromise the structural integrity of the home, leading to potential safety hazards.
Real-life examples of building codes impacting subfloor thickness include:
- Mobile homes in areas prone to high winds or seismic activity may require thicker subfloors to withstand these forces.
- Mobile homes with large floor plans or heavy appliances may need thicker subfloors to support the additional weight.
- Building codes may also specify different subfloor thicknesses for different types of flooring materials, such as tile or carpet.
Understanding the connection between building codes and subfloor thickness is crucial for ensuring the safety and longevity of mobile homes. By adhering to these codes, manufacturers and installers can create structurally sound and durable homes that meet the highest standards of quality and safety.
Manufacturer Specifications
Within the context of "How Thick Is The Subfloor In A Mobile", manufacturer specifications play a crucial role in determining the thickness and structural integrity of the subfloor. These specifications are established by the manufacturers of mobile homes and outline the specific requirements for the subfloor, including its thickness, materials, and installation methods.
- Subfloor Material
Manufacturer specifications outline the type of material used for the subfloor, such as plywood, oriented strand board (OSB), or other engineered wood products. The choice of material affects the thickness, strength, and durability of the subfloor.
- Subfloor Thickness
Manufacturer specifications provide the minimum and recommended thickness for the subfloor. This thickness is determined based on factors such as the size of the mobile home, the expected loads, and the flooring material being used.
- Installation Methods
Manufacturer specifications include detailed instructions for installing the subfloor, including the spacing of joists, the type of fasteners to use, and the proper techniques for securing the subfloor to the frame of the mobile home.
- Compliance with Building Codes
Manufacturer specifications ensure that the subfloor meets or exceeds the minimum requirements of applicable building codes. This helps to ensure the safety and structural integrity of the mobile home.
Overall, manufacturer specifications provide clear and comprehensive guidelines for the design, installation, and maintenance of the subfloor in a mobile home. By following these specifications, manufacturers and installers can ensure that the subfloor meets the highest standards of quality and safety.
Climate Considerations
When determining "How Thick Is The Subfloor In A Mobile", it is crucial to consider the impact of climate conditions. Different climates can pose unique challenges to the subfloor, affecting its thickness, material selection, and installation techniques.
- Temperature Fluctuations
Extreme temperature variations can cause the subfloor to expand or contract, leading to buckling, warping, or cracking. Thicker subfloors are less susceptible to these effects, providing greater stability and reducing the risk of damage.
- Moisture Levels
High humidity or water exposure can cause the subfloor to swell or rot. Thicker subfloors made of moisture-resistant materials, such as pressure-treated lumber or composite panels, can better withstand these conditions.
- Wind Loads
Strong winds can exert significant pressure on the subfloor, especially in coastal areas or regions prone to hurricanes. Thicker subfloors provide greater structural support, reducing the risk of wind damage.
- Seismic Activity
In earthquake-prone areas, a thicker subfloor can provide additional protection against seismic forces, minimizing the risk of damage to the flooring and other structural components.
Understanding the climate considerations related to "How Thick Is The Subfloor In A Mobile" is essential for ensuring the longevity and structural integrity of the home. By selecting an appropriate subfloor thickness and using appropriate materials and installation techniques, manufacturers and installers can create mobile homes that withstand the unique challenges posed by different climates.
Floor Plan
In exploring "How Thick Is The Subfloor In A Mobile", the floor plan plays a pivotal role in determining the appropriate subfloor thickness. The floor plan dictates the layout, size, and weight distribution within the mobile home, which directly impacts the structural requirements of the subfloor.
A larger floor plan, for instance, requires a thicker subfloor to support the increased weight of walls, furniture, and occupants. Additionally, complex floor plans with multiple rooms and load-bearing walls necessitate a more robust subfloor to ensure stability and prevent deflection. Understanding the relationship between floor plan and subfloor thickness is crucial for preventing structural issues, such as sagging floors or uneven surfaces.
Real-life examples of the floor plan's impact on subfloor thickness include:
- Mobile homes with open floor plans often require thicker subfloors to compensate for the absence of supporting walls.
- Floor plans with heavy appliances, such as stoves or refrigerators, necessitate thicker subfloors in those specific areas to bear the concentrated weight.
By considering the floor plan during subfloor selection, manufacturers and installers can create mobile homes with structurally sound and durable floors, ensuring the safety and comfort of occupants.
Maintenance
Within the context of "How Thick Is The Subfloor In A Mobile", maintenance plays a critical role in preserving the integrity and longevity of the subfloor. Regular maintenance can detect and address issues that may affect the thickness and stability of the subfloor, preventing costly repairs or premature replacement.
One of the main causes of subfloor deterioration is moisture damage. Water leaks, plumbing issues, or inadequate ventilation can lead to moisture accumulation, causing the subfloor to swell, warp, or rot. Proper maintenance involves regularly inspecting the subfloor for signs of moisture damage and promptly addressing any leaks or moisture sources.
Real-life examples of maintenance within "How Thick Is The Subfloor In A Mobile" include:
- Regularly checking for and repairing any leaks in plumbing fixtures, roofs, or windows to prevent water damage.
- Maintaining proper ventilation in crawl spaces and underneath the mobile home to prevent moisture buildup.
- Inspecting the subfloor for signs of damage, such as soft spots, buckling, or warping, and addressing any issues promptly.
Understanding the connection between maintenance and subfloor thickness is crucial for mobile homeowners to maintain the structural integrity and safety of their homes. By performing regular maintenance, homeowners can extend the lifespan of their subfloors, reduce the risk of costly repairs, and ensure a comfortable and safe living environment.
Frequently Asked Questions About Subfloor Thickness in Mobile Homes
This section addresses common questions and concerns regarding the thickness of subfloors in mobile homes, providing valuable insights for homeowners and professionals alike.
Question 1: What is the typical thickness range for subfloors in mobile homes?
Answer: Subfloor thickness in mobile homes typically ranges from 1/2 inch to 1 inch, depending on factors such as the size of the home, floor plan, and building codes.
Question 2: Why is subfloor thickness important?
Answer: Subfloor thickness affects the structural integrity, soundproofing, insulation, and overall durability of the mobile home.
Question 3: How does subfloor thickness impact flooring options?
Answer: Thicker subfloors can support heavier flooring materials, such as tile or hardwood, while thinner subfloors may be suitable for lighter options like carpet.
Question 4: Are there specific building codes that regulate subfloor thickness in mobile homes?
Answer: Yes, building codes often specify minimum subfloor thickness requirements to ensure structural safety and compliance.
Question 5: How can I determine the thickness of my mobile home's subfloor?
Answer: You can measure the subfloor thickness by removing a vent cover or cutting a small hole in an inconspicuous area.
Question 6: What are the signs of a damaged or compromised subfloor?
Answer: Signs of subfloor damage include soft spots, buckling, warping, or excessive moisture.
These FAQs provide essential information about subfloor thickness in mobile homes, helping homeowners make informed decisions regarding maintenance, repairs, and upgrades. Understanding the factors that influence subfloor thickness and its impact on the overall structure and durability of the home is crucial for ensuring a safe and comfortable living environment.
In the next section, we will delve deeper into the structural considerations related to subfloor thickness in mobile homes, exploring its role in supporting the weight of the home and its occupants.
Tips for Determining Subfloor Thickness in Mobile Homes
Understanding the thickness of your mobile home's subfloor is crucial for ensuring structural integrity and durability. Here are some practical tips to help you determine the thickness and assess the condition of your subfloor:
Tip 1: Check Building Codes and Manufacturer Specifications
Refer to local building codes and manufacturer specifications for the minimum required subfloor thickness for your mobile home.
Tip 2: Inspect Accessible Areas
Remove vent covers or cut a small hole in an inconspicuous area to measure the subfloor thickness directly.
Tip 3: Look for Signs of Damage
Check for soft spots, buckling, or warping, which may indicate subfloor damage or moisture issues.
Tip 4: Consider Floor Plan and Weight Distribution
Heavier appliances or complex floor plans may require a thicker subfloor for adequate support.
Tip 5: Factor in Climate Conditions
Extreme temperatures, moisture levels, and wind loads can affect subfloor thickness requirements.
Tip 6: Consult a Professional
If you suspect subfloor damage or are unsure about the thickness, seek professional advice from a qualified inspector or contractor.
Tip 7: Maintain Proper Ventilation
Ensuring proper ventilation in crawl spaces and underneath the mobile home helps prevent moisture buildup and subfloor damage.
Tip 8: Address Leaks and Moisture Sources Promptly
Water leaks and plumbing issues can lead to moisture damage, so address them immediately to protect the subfloor.
By following these tips, you can assess the thickness and condition of your mobile home's subfloor, ensuring its structural integrity and longevity. Understanding subfloor thickness is essential for maintaining a safe and comfortable living environment.
In the next section, we will explore the importance of using the correct subfloor thickness for different types of flooring materials. Choosing an appropriate subfloor thickness is crucial for ensuring compatibility with your desired flooring and preventing potential issues.
Conclusion
In exploring "How Thick Is The Subfloor In A Mobile", we have uncovered the intricate relationship between subfloor thickness and the overall integrity, durability, and comfort of mobile homes. Key considerations include structural support, insulation, soundproofing, flooring type, building codes, manufacturer specifications, climate conditions, floor plan, maintenance, and compatibility with different flooring materials.
Understanding the appropriate subfloor thickness for your mobile home ensures a safe and comfortable living environment. By considering factors such as the size of the home, floor plan, flooring material, and climate conditions, you can make informed decisions about subfloor thickness and maintenance.
Anahi parents and siblings who are enrique manuel
Kalani hilliker ethnicity nationality race family body measurements
How much money does matt burch make latest
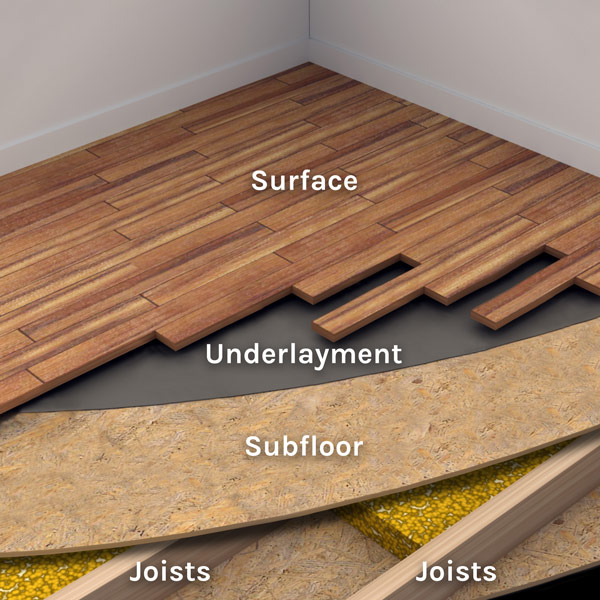

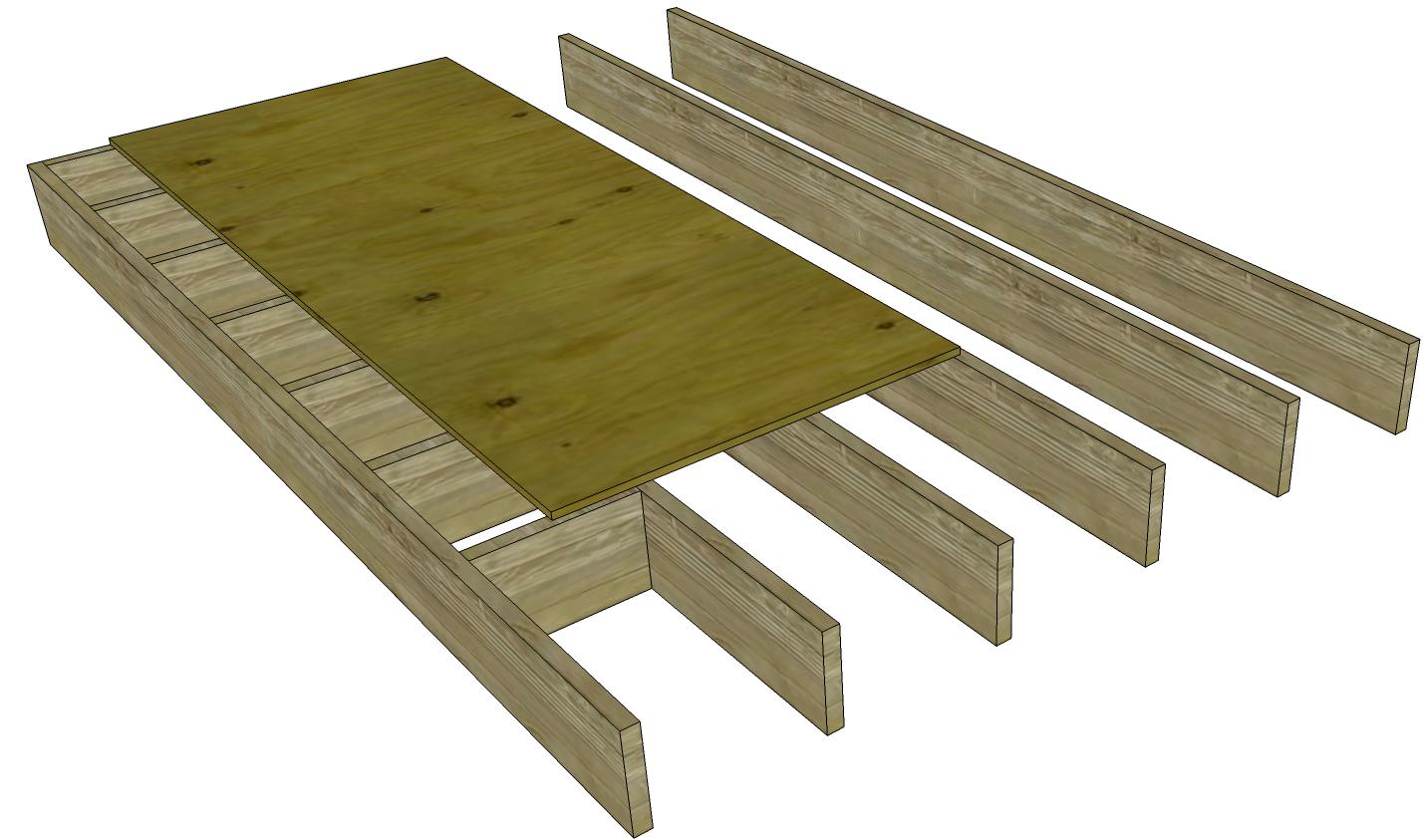
ncG1vNJzZmiZnJyyonrSn6ZrZpSetKrAwKWmnJ2Ro8CxrcKeqmebn6J8qbvWZquhoZOgeqq%2FjK2fnmWjqq%2BnuM6oqWahnmKubrnOm6ClnV6dwa64